- December 5, 2021
- Posted by: workflick workflick
- Category: Uncategorized

A Guide to Reverse Logistics: How It Works, Types and Strategies
- January 14, 2021
- Posted by: Cliff Locks
- Category: Uncategorized
Learn everything you need to know about reverse logistics, including the types of logistics, the process involved, steps, benefits, challenges and how to use reverse logistics to create value for your business. Plus, get advice on what it takes to be successful at reverse logistics and reduce the costs that come with returned products.
In this article:
- Reverse logistics explained step by step
- Six strategies to optimize reverse logistics
- Reverse logistics and the supply chain
What Is Reverse Logistics?
Reverse logistics is a type of supply chain management that moves goods from customers back to the sellers or manufacturers. Once a customer receives a product, processes such as returns or recycling require reverse logistics.
Reverse logistics start at the end consumer, moving backward through the supply chain to the distributor or from the distributor to the manufacturer. Reverse logistics can also include processes where the end consumer is responsible for the final disposal of the product, including recycling, refurbishing or resale.
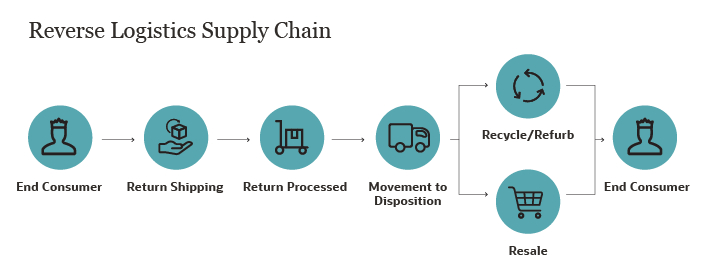
When Is Reverse Logistics Used?
Organizations use reverse logistics when goods move from their destination back through the supply chain to the seller and potentially back to the suppliers. The goal is to regain value from the product or dispose of it. Worldwide, returns are worth almost a trillion dollars annually and have become increasingly common with the growth of ecommerce.
The objectives of reverse logistics are to recoup value and ensure repeat customers. Less than 10% of in-store purchases are returned, compared to at least 30% of items ordered online. Savvy companies use reverse logistics to build customer loyalty and repeat business and to minimize losses related to returns.
Reverse Logistics vs. Traditional Logistics
Traditional product flow starts with suppliers and moves on to a factory or distributor. From there, the goods go to retailers and customers. Reverse logistics management starts at the consumer and, moving in the opposite direction, returns products to any point along the supply chain.
Well-designed supply chains are responsive to changes and can handle some reverse logistics requirements. This reverse process can return products one step back in the chain or to the original supplier. They can even send returned products back to regular sales or discount channels (like liquidators).
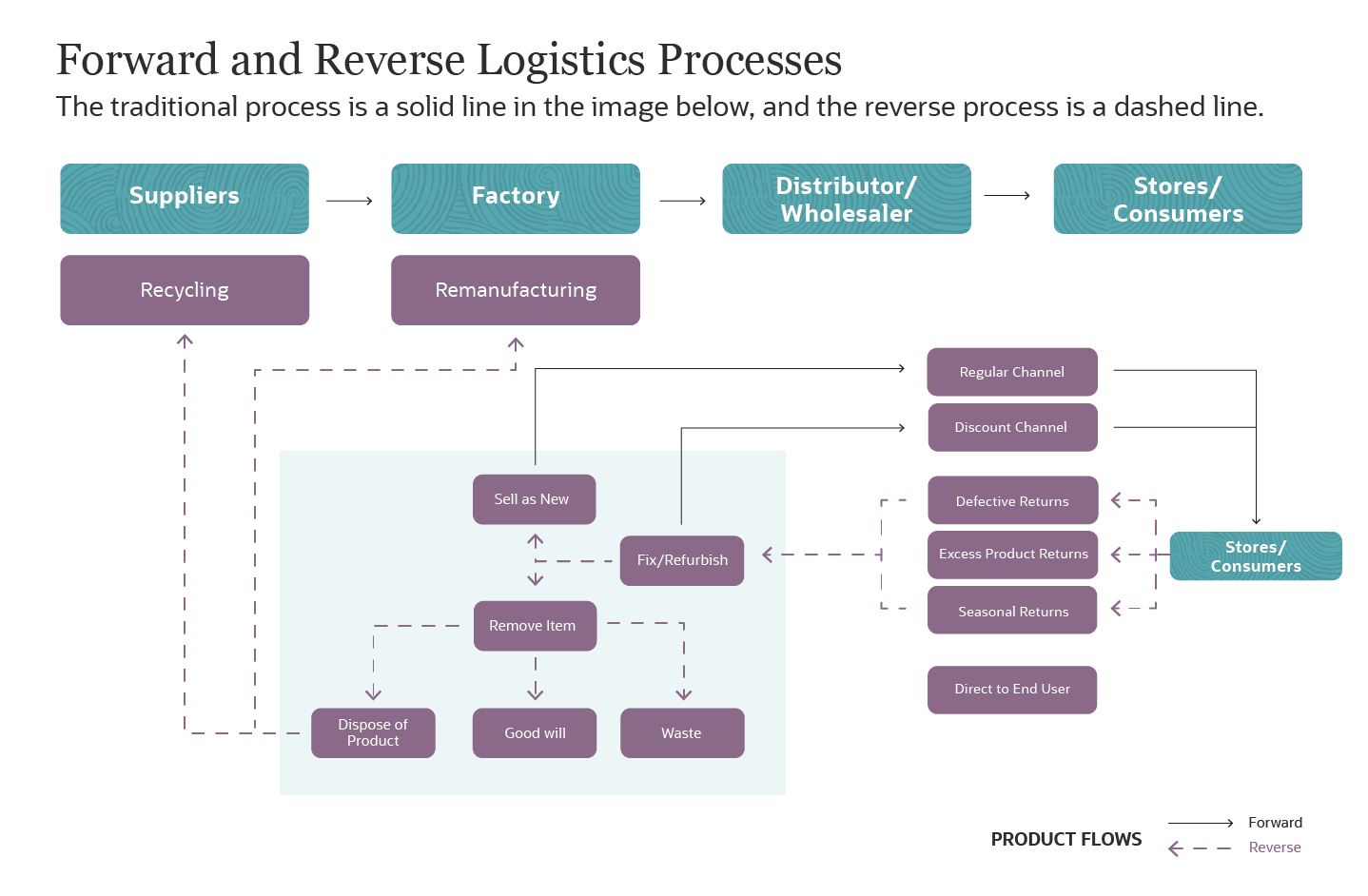
How Reverse Logistics Works
Reverse logistics moves goods from the traditional endpoint of the supply chain at least one step backward. This process can involve various plans and controls. Some companies prefer to outsource this work.
Reverse Logistics Process
The reverse logistics process involves managing returns and buying surplus goods and materials. The process is also responsible for dealing with any leases or refurbishments. Reverse logistics vary across different industries, and there are different economic incentives for improving reverse logistics management.
For example, in the beverage industry, the reverse logistics process uses empty tap containers. Beverage production companies want to recapture the value of their containers by reusing them. This requires planning transportation, managing shipping loads and cleaning the containers.
In the construction industry, reverse logistics moves and recycles salvaged materials to new sites. As the construction industry adopts more sustainable practices to reduce waste, there is an opportunity for cost savings by using reverse logistics.
In the food industry, reverse logistics is responsible for returning packaging materials and pallets. Companies also must deal with rejected food shipments. Rejections can create logistical challenges due to delays that lead to food spoilage and concerns over tampering. The Reverse Logistics Association is developing secure, quick, reliable, login (SQRL) codes on packaging to provide detailed product information and address these logistical challenges.
5 Steps to Good Reverse Logistics
- Process the Return
The return process starts when the consumer signals they want to return a product. This step should include return authorization and identify the product’s condition. This process also involves scheduling return shipments, approving refunds and replacing faulty goods. - Deal with Returns
Once a returned product arrives at your location or centralized processing center, inspect it and determine its return category. (Note: If you have optimized reverse logistics, you should know where the product should go before it arrives.) Sort products into the disposition options: fix, resell as new, resell as a return, recycle, scrap or refurbish. - Keep Returns Moving
Reduce your daily waste by sending repairable items to the repair department. - Repair
After reviewing the returned item/equipment and determining whether it can be repaired, move it to the repair area. If not possible, sell any sellable parts. - Recycle
Any parts or products that you cannot fix, reuse or resell should be sent to the area for recycling.
Types of Reverse Logistics
The different types of reverse logistics are also known as reverse logistics components. They focus on returns management and return policies and procedures (RPP) and account for remanufacturing, packaging, unsold goods and delivery issues. Other types of reverse logistics account for leases, repairs and product retirement.
Reverse Logistics Components:
- Returns management: This process deals with product returns from customers or avoiding returns in the first place. These activities should be fast, controllable, visible and straightforward. Customers judge a company on its return flow and re-return policies. A re-return is the return of an item a second time. Often, these returns trigger the extended return policies, such as offering store credit. For example, a customer buys a returned product on clearance, takes it home and discovers it broken. The store policy would not normally accept the return, but it does allow for a store credit for the faulty product. A re-return can also occur when a vendor rejects the return and gives it back to the purchaser without a refund. This scenario could happen with custom-made items.
- Return policy and procedure (RPP): The policies about returns that a company shares with customers is its RPP. These policies should be visible and consistent. Employees should also adhere to them.
- Remanufacturing or refurbishment: Another type of reverse logistics management includes remanufacturing, refurbishing and reconditioning. These activities repair, rebuild and rework products. Companies recover interchangeable, reusable parts or materials from other products, also known as the cannibalization of parts. Reconditioning involves taking apart, cleaning and reassembling products.
- Packaging management: This type of reverse logistics focuses on reuse of packing materials to reduce waste and the disposal.
- Unsold goods: Reverse logistics for unsold goods handles returns from retailers to manufacturers or distributors. These types of returns can be due to poor sales, inventory obsolescence or a delivery refusal.
- End-of-life (EOL): When a product is EOL, it is no longer useful or does not work. The product may no longer meet a customer’s needs or be replaced by a newer, better version. Manufacturers often recycle or dispose of products that are end-of-life. These goods can create environmental challenges for manufacturers and countries.
- Delivery failure: With failed deliveries, drivers return products to sorting centers. From there, the sorting centers return the products to their point of origin. While rare, some sorting centers may have the staff available to identify why a delivery failed, correct the problem and resend.
- Rentals and leasing: When a piece of equipment comes to the end of its lease or rental contract, the company that owns the product can remarket, recycle or redeploy it.
- Repairs and maintenance: In some product agreements, customers and companies maintain equipment or repair it if issues arise. In some cases, the company sells damaged returned products to another consumer after repair.
What Are the Five Rs of Reverse Logistics?
The five Rs of reverse logistics are returns, reselling, repairs, repackaging and recycling. Companies apply metrics to each of these options to track improvement and success. Your business may want to take a closer look at the Five Rs to streamline its reverse logistics processes and reduce losses there.
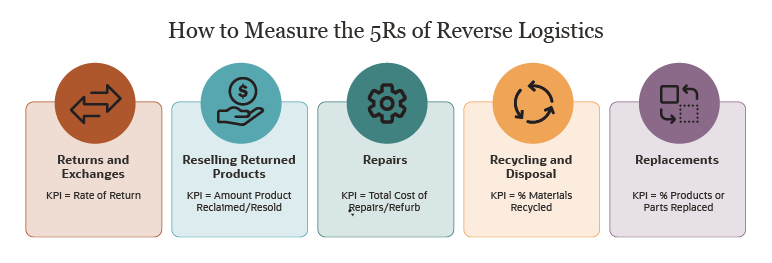
Reverse Logistics Examples
Globally, companies are changing the ways they address waste, and the supply chain is a big piece of that initiative. These reverse logistics examples focus on returns, exchanges and recycling.
People are more likely to buy products from a company if they think returns are easy and they are even more likely to become repeat customers if they’ve had a good return experience. For example, Home Depot offers reverse logistics help for online purchases via its website. In 2020, the company’s online sales represented almost 15% of total sales. When a customer returns goods, they have a choice: send products back by printing a shipping label, or drop them off in-store. These items are then sent to Home Depot reverse logistics centers that handle damaged and misdirected products.
Retailer Levi Strauss uses reverse logistics to improve sustainability in textiles. The business repurposes jeans or recovers and reprocesses the fibers into raw materials to make new jeans. By partnering with other companies for repurposing, Levi Strauss can produce reconstructed jeans at a higher price point.
Kohl’s, a major retailer with more than 1,000 brick-and-mortar stores, is another example of the reverse supply chain in action. Kohl’s partners with Amazon to accept, screen and send back Amazon returns in a single shipment. Customers who prefer returning products in-person benefit from this relationship and Kohl’s gets customers in its door who may not normally visit its stores. Kohl’s also carries some Amazon products and can simply return them if they do not sell.
Some big brands are also turning to reverse logistics to address waste. Proctor & Gamble, PepsiCo, and Unilever are shifting to reusable packaging that consumers can return. The companies will clean and use the containers again. Transportation and logistics are evolving for these companies and will pick-up the packaging when they drop off products.
Some companies, such as GE Healthcare and Cisco, specialize in refurbishing, repairing and remanufacturing defective or out-of-date goods for consumers. Cisco remanufactures goods such as phones, routers and switches. GE Healthcare remanufactures imaging devices and ultrasound machines.
Microsoft has a large global initiative to deal with end-of-life for devices, batteries and packaging. Microsoft’s product packaging is 100% recyclable, and it has a program for refurbishing and reusing personal computers.
Some organizations resell overstocked goods to the secondary market, like factory outlets, off-price and discount stores, and online auction sites. Retailers such as TJX Companies (TJ Maxx, Marshalls and HomeGoods) buy these overstock items and sell them at a discounted price to consumers.
Find more examples of how companies are making returns work for them with reverse logistics.
Importance of Reverse Logistics to Your Business
Reverse logistics is important because it maintains an efficient flow of goods. The process reduces costs, creates value, decreases risk and completes the product life cycle.
Gartner Research says that about 70% of businesses plan to invest in the “circular economy.” This circular economy follows traditional logistics and then continues around through what Gartner calls a closed-loop supply chain.
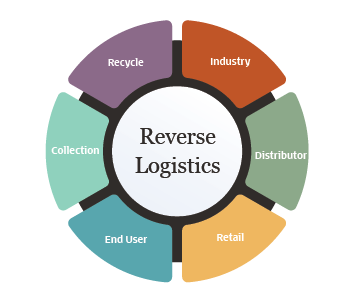
With this practice, companies are participating in a system focused on a sustainable economy. Companies find new uses for disposed products with recovery, repair and recycling. Materials once typically viewed as waste have value again.
The circular economy also ensures compliance as many countries institute a policy requiring “producers” to develop more sustainable practices. The guidelines outline subsidies for waste prevention, research and development and recycling. Other policies restrict landfills, mandate collection and recycling programs, and penalize certain waste practices.
How Does Reverse Logistics Create Value?
Reverse logistics creates value by turning waste into sales and builds customer trust. Businesses resell, reuse and recycle returned products. In addition, effective reverse logistics keeps down any storage and distribution costs.
Gartner Research finds that less than half of returned goods are resold at their full price. There is value in finding the best disposition option for returned items. For example, retail businesses like B-Stock resell returned goods. B-Stock sold 70 million returned or excess goods in 2019. The company buys the returns for a percentage of their original cost and then resells them at a discount to the consumer.
Using reverse logistics to boost the efficiency of the traditional supply chain benefits everyone. Some businesses separate their forward and reverse logistics, and others combine them. The relative success of combining them depends on the company’s experience, the value of its products and return volume. Either way, they use practices to maximize their profitability ratios with their supply chain activities. Read these expert tips on how to maximize profits in business.
Benefits of Optimized Reverse Logistics
Optimized reverse logistics produce financial benefits while positively impacting the environment and business culture. Refining the processes for what happens to products after delivery helps retain customers and save money.
The product data collected when engaging with customers after delivery is an advantage of well-executed reverse logistics. Data provides insight into an organization’s supply chain and an opportunity to improve products and/or the customer experience.
Optimized reverse logistics also leads to better supply chain visibility, which leads to benefits like:
- Cost reduction
- Greater customer satisfaction
- Better customer retention
- Faster and better service
- Loss reduction
- Improved brand sentiment
- Waste reduction and greater sustainability
Challenges of Reverse Logistics
A challenge of reverse logistics is that the flow must be bi-directional. Managers need to set up the right infrastructure for it to be effective. That often requires software that can automate and track every step of reverse logistics. Additionally, once that infrastructure is in place, management needs to continually monitor and evaluate the organization’s reverse logistics processes to ensure efficiency.
Companies must track inbound and outbound logistics to get the full picture. Inbound logistics manages the receipt of raw materials or goods from the supplier to the manufacturer. Outbound logistics is the processes that deliver the finished goods to the end user. Both inbound and outbound logistics are measured from the manufacturer’s perspective, while reverse logistics can be part of any point in the supply chain.
7 Strategies to Optimize Reverse Logistics
To optimize reverse logistics, companies need cohesive strategies that account for speed, efficiency and cost. When taking action, consider policies, partners, data, capacity, logistics and transportation.
The seven strategic ways to optimize reverse logistics are:
- Evaluate Relevant Policies and Agreements
Review and revise the procedures related to your company’s returns and repairs. These policies should be clear and consider the root causes of returns and repairs. The way a company deals with returns and repairs can be competitive differentiators. - Collaborate with Suppliers
Close collaboration with suppliers can help ensure a smooth, integrated experience for customers, not a disjointed one they will struggle to navigate. - Use Data to Optimize Processes
By collecting data on product returns, you can understand why customers may be returning products. Then, you can make adjustments in sales, product design and forward logistics processes accordingly. - Track products forward and backwards
Linking raw materials to the finished good and the customer order allows you to trace ingredients in the event that you need to process recalls—instead of issuing them for entire lines, you can find the issue and selectively issue recalls. - Centralize Return Centers
With a centralized return center, you can better sort products and identify the best next step for each of them. With a center, businesses can more efficiently determine how best to reclaim product value. If your company lacks the resources to have a separate returns center, consider dedicating a portion of your warehouse or factory to returns. - Examine Logistics and Transportation
Regularly review the processes for forward and reverse logistics and transportation. Determine if it is feasible to integrate some of these processes and transit. For example, if your delivery drivers can pick up empty pallets as they drop off full pallets, you save trips, time and money. - Automate
Use cloud-based logistics software to help streamline operations. For example, a software system can track asset recovery, manage refurbishment and provide business intelligence analytics.
How Do Reverse Logistics Impact Supply Chain Management?
Reverse logistics provide another critical opportunity for supply chain optimization. Supply chain management accounts for the reverse and forward flow of goods, and a surge of returns can drive up supply chain costs, harming profitability.
What Is Reverse Logistics vs. Reverse Supply Chain?
The reverse supply chain is the backward movement of goods (such as defective products) from vendors back up the supply chain. It is the opposite of the typical supply chain, where items go from manufacturer to retailer to consumer.
Reverse logistics refers to everything related to returns and what happens to those products after the consumer takes them back. That includes planning and implementing strategies to reduce costs and losses related to returns and to build a better returns experience.
Monitoring Reverse Logistics in Your Supply Chain
Companies monitor reverse logistics in the supply chain to find better ways to process and dispose of products. There is a considerable volume of information available in the ways goods move back and forth through the supply chain. This detail can help companies meet their delivery goals.
Some organizations have the simple goal of on-time delivery; others reach for what they call the “perfect order.” For every order, the goal is to get a perfect score in place, time, condition, package, quantity, documentation, customer and invoice. The only way to achieve a perfect order is to monitor the data, develop metric targets and improve processes based on your results. Reverse logistics can play a central role in delivering the perfect order.
5 Key Reverse Logistics Supply Chain Metrics to Monitor and Confirm
There are five key reverse logistics-focused supply chain metrics that will help increase asset recovery. Supply chain analytics can help management make data-driven decisions at all steps of the supply chain.
Key supply chain metrics include:
- Volume: The volume of products returned and subsequently resold, reused and recycled is a top metric used to track reverse logistics. Companies should use these measurements to identify missed opportunities or problems and determine where process improvements can make a difference.
- Percent of Costs: Compare the costs attributed to resales, refurbishing, reuse and recycling to the total supply chain cost. Determine the difference in the price of these activities versus the cost of returns. Be sure to calculate the percent of expenses recovered by item.
- Condition of Returned Products: Some products come back in perfect resale condition, and companies can turn them around for resale at full value. Other goods may need some work before a company can resell them. In that scenario, companies should consider other sales channels for those products. For example, companies may sell refurbished electronics through another sales channel. Determine the cost of materials and workmanship to determine the full value. Review the percent of items sent to each sales channel and whether the company is recouping enough money.
- Financial Value: Each part of the supply chain has economic value. Understanding what financial stake your company has in each step can lead to better processes and efficiencies.
- Errors: Every step in the supply chain also has the potential for errors, such as unaccepted deliveries or defective materials. Review the cost of mistakes and how frequently they occur to identify opportunities for improvement.
Supply chain analytics should exist throughout the entire value chain, from sourcing materials through distribution and delivery. Useful metrics lead to growth in revenue, better margins and controlled capital. Supply chains are increasingly going digital, so collecting the data is easier. Read the supply chain analytics guide to learn how to make the most of this practice.
The Future of Reverse Logistics
The future of reverse logistics is all about minimizing disruptions from returns. Especially in ecommerce, and increasingly in the retail industry, the volume of returns is increasing. Companies can use reverse logistics to integrate all parts of the returns process.
One way to integrate returns is to connect the product’s data to how staff needs to handle it. Documenting what happens to a returned product—whether the item will go to resale, repairs, or be recused for raw goods—the supply chain can support this integration. The future of reverse logistics involves integrated supply chain management software that helps make these determinations and can also provide valuable reports.
Manage Reverse Logistics with Warehouse Management Software
Managing your reverse logistics is essential for the bottom line and reputation of your business. Consumers need to feel like they are buying products from companies with integrity, and improving your reverse logistics opens up opportunities for a number of sustainable business practices.
That’s why it is crucial to have a warehouse management system (WMS) that can manage inbound and outbound logistics and deliver analytics in real time. Businesses need insights across transportation and logistics providers, through warehouse and fulfillment and ultimately need to integrate all that information with financial data in an enterprise resource planning (ERP) system. ERP platforms like NetSuite, paired with a warehouse management system, allow companies to easily track returns, monitor the movement of goods, issue credits through the accounting system and update everything in the customer record.
Similarly, inventory management is key to efficient returns processes. A high rate of returns can lead to inventory buildup, and an effective inventory management system will alert you when inventory levels are growing too quickly—faster than your rate of sales.
Many companies are taking a closer look at their reverse logistics as they realize returns are a major source of expenses and there are opportunities to recover more money on those goods. Additionally, rising return rates make it imperative for these businesses to figure out a more cost-effective way to handle products sent back to them. Evaluating your reverse logistics processes to identify inefficiencies and address those shortcoming can boost your bottom line by not only lowering costs, but increasing customer loyalty and elevating brand reputation.
Reverse Logistics FAQ
You may have additional questions about reverse logistics. Below, we answer some of the most popular ones.
What is integrated logistics?
Integrated logistics is the full process that covers delivery through end-user issues and then deals with product disposition. Integrated logistics stresses material and resource sustainability.
How much does it cost to implement a reverse logistics plan?
Implementing a reverse logistics plan costs about 7-10% of the cost of goods in a company. However, it’s worth noting that reverse logistics planning should bring down the costs associated with returns.
How does reverse logistics work in the pharmaceutical industry?
In the pharmaceutical industry, reverse logistics helps keep medicines safe (out of landfills and water supplies). The sector handles product returns and disposal through third-party companies and distributors.
Can you explain the role of reverse logistics in the service industry?
In the service industry, reverse logistics helps address repairs more quickly. Best practices include refunds, warranty work and credit. Working out these policies keeps customers happy.
How does reverse logistics differ for the manufacturing and service industries?
The service and manufacturing industries differ from others. Their products and services are not standard, so the returns are not standard. The reverse logistics process starts after the company fixes the service or manufacturing part.
Manufacturing companies sell fixed parts as refurbished items. These parts have a lower value and may go through a different supply chain. In the service industry, companies can provide warranty work, credit, or work refunds.
How can ecommerce organizations handle reverse logistics to ensure it’s a low-cost transaction?
To make returns a low-cost transaction, ecommerce companies should combine returns with deliveries. They should also consider turning to third-party partners. Ecommerce businesses should identify the root causes of problems and develop strategies to decrease these issues.
What is a reverse logistics expert?
A reverse logistics expert is a professional who can help your company be more efficient by suggesting and implementing process improvements in your reverse supply chain. Good reverse logistics experts consider your customers, business priorities and sales goals.
How are forward logistics and reverse logistics different?
The difference between reverse and forward logistics is the direction the product is moving along the supply chain. Products that come from the manufacturer and move toward the customer are going forward. Products coming back from customers to retailers or manufacturers are heading in reverse.
What is reverse distribution?
Reverse distribution is the role of removing goods that are unsold, damaged, expired or recalled from retailers. Like with returns, these goods go in the reverse direction through the supply chain.
What is design for logistics (DFL)?
The concept of DFL states that products and their packaging design can lower the expenses related to logistics. For example, soda cans became flat on top, making them easier and cheaper to transport and store.
What is design for reverse logistics (DFRL)?
DFRL refers to designing products and packaging that makes it cheaper and easier to move in a reverse flow in the supply chain. For example, manufacturers package products in reusable canisters that they refill for retailers.
How does reverse logistics reduce business risk?
Reverse logistics reduce business risk by ensuring companies adhere to policies for waste and disposal. Some governments fine companies that do not meet guidelines. Reverse logistics also help companies recoup value in unsold and returned goods.
How do you lower the cost of reverse logistics?
Cut the costs in reverse logistics by first decreasing returns. Experts recommend enabling customer product reviews to help set expectations and reduce returns. Then, look for ways to combine reverse and forward logistics to drive cost savings.
How does reverse logistics contribute to a lean supply chain?
A solid reverse logistics plan reduces waste. Lean principles can also make the supply chain more efficient. Instead of separating shipping and returns, a lean supply chain combines them.
Authors: Abby Jenkins | Product Marketing Manager at Oracle / NetSuite
Product Return Solutions
How can we help you?
Contact us to start working together ensures you’ll have clarity on the best practices in Reverse Logistics, which will ease the pain and reduce product returns.
Clifford Locks
Founder and President of Reverse Logistics Solutions
I have worked with Cliff over the past 3 years on a wide array of projects and I have been impressed with each and every project he has worked on for me! His recommendations are insightful and actionable. He is a very reasonable person and considers constraints when giving business advice.
-President and CEO
“You played a large part in helping us to achieve our goals. You were able to maintain some degree of order while allowing all the participants to contribute in a way in which they felt recognized and their input valued…. Your perseverance would not allow us to rest on our insights. We appreciate your gentle insistence on our devising a concrete plan of action.”
– First Vice President
“Cliff really is insightful and a good mediator. He offers a really good forum for us to meet weekly to discuss short & long term goals. I find that I hear things from my associate that I didn’t know he was thinking. It’s an organized weekly phone call … geared toward corporate direction and individual leadership growth. Cliff … draws the answer and direction out of each client and helps them move themselves forward. The weekly consistency really drives the process forward effectively.”
– President
Looking for a First-Class Reverse Logistics Consulting Solution?
Pricing for inside
To best practices for continuous innovation